Ultimate Guide to Choosing the Right Die Casting Mold Supplier
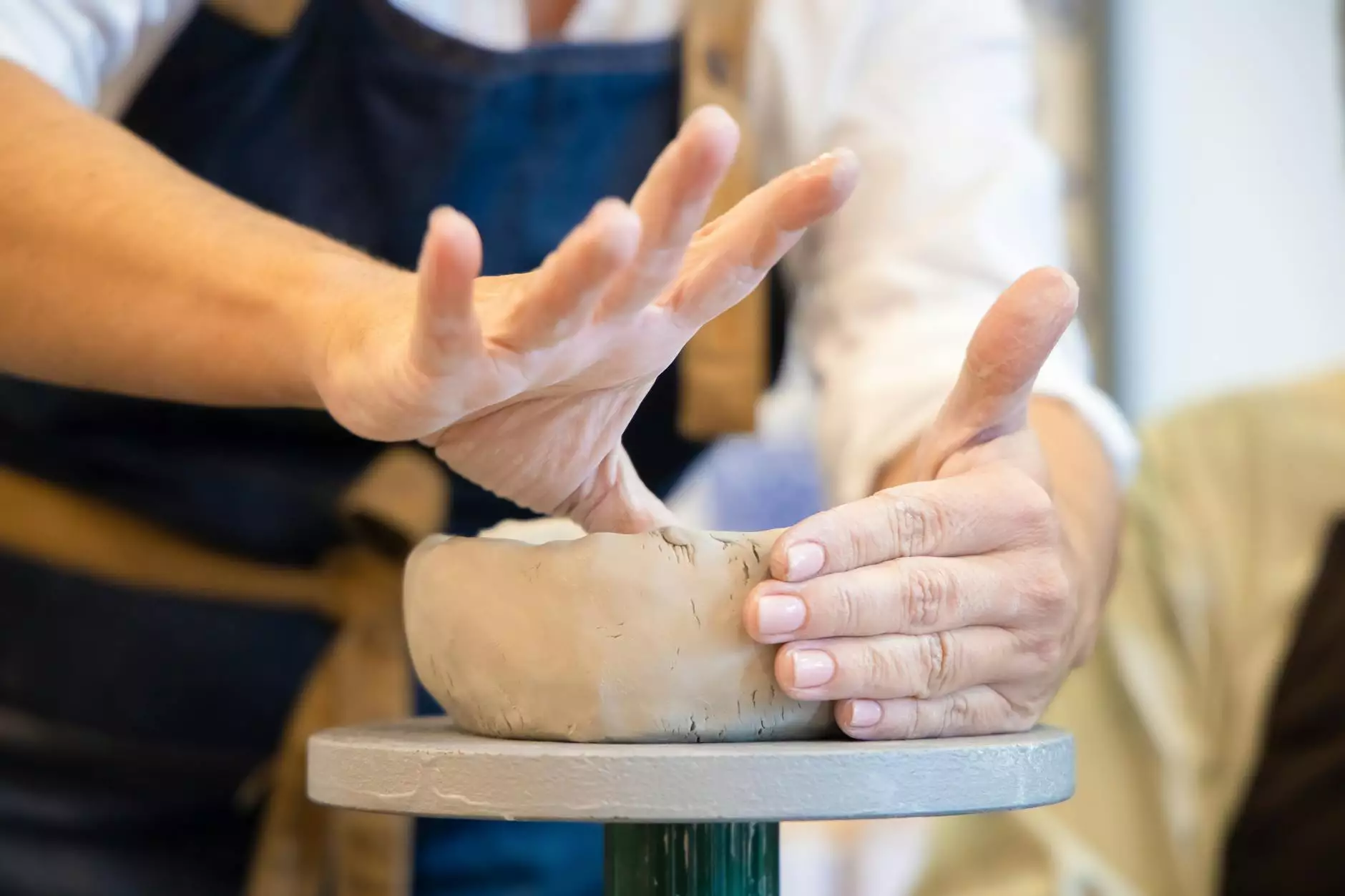
In the competitive world of manufacturing, understanding the complexities of metal fabrication is crucial for any business aiming to excel. As a pivotal component of this industry, die casting molds play a significant role in the efficiency, precision, and quality of the final products. This comprehensive guide will explore how to select the finest die casting mold supplier to meet your business needs, with a focus on quality, capability, and reliability.
What is Die Casting?
Die casting is a manufacturing process that involves forcing molten metal into a mold cavity under high pressure. This process is used to create complex shapes with highly accurate dimensions. The molds, which are typically made from steel or iron, are designed to withstand the high pressures of the molten metal during casting.
The Advantages of Die Casting
- High Efficiency: Rapid production rates make die casting ideal for high-volume production.
- Excellent Precision: Die casting provides excellent dimensional accuracy and smooth surfaces.
- Material Versatility: Suitable for various metals, including aluminum, zinc, and magnesium.
Why Selecting the Right Supplier Matters
Choosing the correct die casting mold supplier is essential for ensuring the success of your manufacturing operations. The right supplier will significantly influence the quality of your parts, delivery times, and overall manufacturing efficiency.
Factors to Consider When Choosing a Die Casting Mold Supplier
- Experience and Reputation
It's essential to partner with a supplier who has a proven track record in the industry. Look for suppliers with years of experience and positive testimonials from clients.
- Production Capabilities
A supplier's production capabilities directly impact lead times and flexibility. Ensure that they can meet your volume requirements and accommodate design changes.
- Quality Control Processes
Inquire about the quality control mechanisms the supplier has in place. This includes certifications, inspection processes, and adherence to international standards.
- Technical Expertise
A knowledgeable team can provide valuable insights into design and material choices, ultimately improving the performance and cost-effectiveness of your molds.
- Cost-Effectiveness
While price is a factor, it should not be the only consideration. Analyze the total value proposition, including quality, service, and support.
Where to Find Reliable Die Casting Mold Suppliers
Finding a reputable die casting mold supplier can be challenging, but several avenues can aid in your search:
- Industry Associations: Join associations or trade groups related to die casting and metal fabrication to connect with members who may provide referrals.
- Online Directories: Utilize online business directories that specialize in manufacturing suppliers are a great resource to identify potential suppliers.
- Trade Shows: Attending industry trade shows is an excellent way to meet suppliers face-to-face and evaluate their capabilities firsthand.
- Referrals: Ask for recommendations from colleagues or industry peers who have had positive experiences with die casting suppliers.
Case Studies: Success Stories from Top Die Casting Mold Suppliers
Examining successful case studies can provide insights into how top die casting mold suppliers operate effectively to satisfy their clients. Here are a few examples:
Case Study 1: Innovations in Design
A major automotive manufacturer partnered with a die casting supplier that specialized in innovative mold design. By leveraging advanced simulation technology, the supplier was able to optimize the mold structure, resulting in a 15% reduction in cycle time and significant material savings, leading to an overall cost reduction of 10% for the client.
Case Study 2: Meeting Tight Deadlines
A consumer electronics company faced a tight deadline for their product launch. They turned to a die casting mold supplier known for its rapid prototyping capabilities. The supplier not only met the deadlines but also maintained quality standards, which resulted in a successful product launch and continued partnership.
Quality Standards in Die Casting
Quality should be the foremost priority when selecting a die casting mold supplier. Various standards apply within the industry, which include:
- ISO 9001: A globally recognized standard for quality management systems.
- IATF 16949: Specific to the automotive sector, focusing on continuous improvement and reduction of variation.
- ASTM Standards: Various standards that focus on the performance and manufacturing processes of metals used in die casting.
Emerging Trends in Die Casting
The die casting industry is evolving, with several emerging trends shaping the future of manufacturing. Staying informed about these trends can influence your choice of supplier:
1. Automation and Industry 4.0
Many suppliers are adopting automation technologies and smart manufacturing practices to improve efficiency. Investing in suppliers that embrace these advancements can enhance your production process.
2. Sustainable Practices
With increasing environmental concerns, many die casting mold suppliers are incorporating sustainable practices into their operations, such as recycling materials and reducing waste. Partnering with eco-friendly suppliers can enhance your brand's reputation.
3. Advanced Materials
Development and use of advanced materials, including lightweight alloys, are on the rise. Suppliers with expertise in these materials can provide innovative solutions tailored for specific industries like aerospace and automotive.
Building a Lasting Relationship with Your Supplier
Once you’ve selected a die casting mold supplier, it's essential to foster a strong partnership. Here are some best practices:
- Open Communication: Maintain regular communication to discuss potential challenges and solutions.
- Feedback and Collaboration: Provide constructive feedback and collaborate on design improvements and innovations.
- Long-Term Vision: Align your business objectives with your supplier to ensure mutual growth and success.
Conclusion
Choosing the right die casting mold supplier is a critical decision that can profoundly impact your business's manufacturing capabilities. By considering factors such as experience, quality control, and technological advancements, you can find a partner that not only meets but exceeds your expectations. With the rapidly changing landscape of metal fabrication, staying informed and adaptable is key to long-term success.
Get Started!
If you are looking for a trusted die casting mold supplier, consider DeepMould. With years of industry expertise, a commitment to quality, and a focus on customer satisfaction, they are equipped to meet all your die casting needs.